近年、新エネルギー産業の急速な発展のおかげで、レーザー溶接はその高速かつ安定した利点により、新エネルギー産業全体に急速に浸透しています。中でもレーザー溶接装置は新エネルギー産業全体の中で最も高い割合を占めています。
レーザー溶接速度が速く、深さが大きく、変形が小さいため、すぐにあらゆる分野で最初の選択肢になりました。スポット溶接から突合せ溶接、肉盛溶接、シール溶接まで、レーザー溶接比類のない精度と制御を提供します。軍事産業、医療、航空宇宙、3C自動車部品、機械板金、新エネルギー、その他の産業を含む工業生産と製造において重要な役割を果たしています。
他の溶接技術と比較すると、レーザー溶接には特有の長所と短所があります。
アドバンテージ:
1. 速度が速く、深さが大きく、変形が小さい。
2. 常温または特殊条件下での溶接が可能であり、溶接設備も簡単です。たとえば、レーザービームは電磁場中ではドリフトしません。レーザーは、真空、空気、または特定のガス環境で溶接でき、ガラスを透過する材料やレーザー光線に対して透明な材料を溶接できます。
3. チタンや石英などの耐火物を溶接でき、異種材料の溶接も良好な結果が得られます。
4. レーザーの焦点が合った後、出力密度は高くなります。アスペクト比は 5:1 に達する可能性があり、高出力デバイスを溶接する場合は最大 10:1 に達する可能性があります。
5. 微細溶接が可能です。レーザービームの焦点を合わせた後、小さなスポットが得られ、正確に位置決めすることができます。微小ワークの組立や溶接に適用し、自動量産を実現します。
6. 手の届きにくい箇所の溶接や、非接触での長距離溶接も柔軟に行えます。特に近年はYAGレーザー加工技術に光ファイバー伝送技術が導入され、レーザー溶接技術の普及・応用が進んでいます。
7. レーザービームは時間的および空間的に分割しやすく、複数のビームを複数の場所で同時に処理できるため、より正確な溶接のための条件が提供されます。
欠陥:
1. ワークの組立精度は高いことが要求され、ワーク上のビームの位置が大きくずれることはできません。これは、集光後のレーザースポットサイズが小さく、溶接線が狭いため、溶加材の追加が困難であるためです。ワークの組み立て精度やビームの位置決め精度が要求を満たさないと、溶接不良が発生しやすくなります。
2. レーザーおよび関連システムのコストが高く、一度の投資が多額です。
一般的なレーザー溶接の欠陥リチウム電池製造において
1. 溶接気孔率
よくある欠陥レーザー溶接毛穴です。溶接の溶融池は深くて狭いです。レーザー溶接プロセス中に、窒素が外部から溶融池に侵入します。金属の冷却および凝固プロセス中に、温度の低下とともに窒素の溶解度が減少します。溶融池金属が冷えて結晶化し始めると、溶解度は急激に低下します。このとき、多量のガスが析出し、泡が発生します。気泡の浮上速度が金属の結晶化速度よりも遅いと気孔が発生します。
リチウム電池産業での応用では、特に正極の溶接時に気孔が発生しやすいが、負極の溶接時には気孔が発生することはほとんどありません。これは、正極がアルミニウムでできており、負極が銅でできているためです。溶接時、内部のガスが完全に溢れ出す前に表面の液体アルミニウムが凝縮するため、ガスが溢れ出て大小の穴ができるのを防ぎます。小さな気孔。
毛穴には上記の原因以外にも、外気、水分、表面の油分などが含まれます。また、窒素の吹き込みの方向や角度も毛穴の形成に影響します。
溶接ポアの発生を抑えるにはどうすればよいでしょうか?
まず、その前に溶接、入荷する材料の表面にある油汚れや不純物は、時間内に洗浄する必要があります。リチウム電池の製造では、入荷した材料の検査が不可欠なプロセスです。
第二に、シールドガス流量は、溶接速度、出力、位置などの要因に応じて調整する必要があり、大きすぎたり小さすぎたりしてはなりません。保護マントの圧力は、レーザー出力や焦点位置などの要因に応じて調整する必要があり、高すぎても低すぎてもいけません。保護マントが溶接部を均一に覆うことができるように、溶接部の形状、方向などに応じて保護マントのノズルの形状を調整する必要があります。
第三に、作業場の空気中の温度、湿度、粉塵を管理します。周囲の温度と湿度は、基板の表面の水分含有量と保護ガスに影響を与え、それがひいては溶融池内での水蒸気の生成と放出に影響を与えます。周囲の温度と湿度が高すぎると、基板の表面と保護ガスの水分が多すぎて、多量の水蒸気が発生し、細孔が発生します。周囲の温度と湿度が低すぎる場合、基板の表面およびシールドガス中の水分が少なすぎるため、水蒸気の発生が減少し、それによって細孔が減少します。品質担当者に溶接ステーションの温度、湿度、粉塵の目標値を検出させます。
第四に、ビームスイング法は、レーザー深溶け込み溶接における気孔を減少または除去するために使用されます。溶接中にスイングが追加されるため、溶接シームに対するビームの往復スイングにより溶接シームの一部が繰り返し再溶融し、溶接池内の液体金属の滞留時間が長くなります。同時に、ビームのたわみにより単位面積あたりの入熱量も増加します。溶接部の深さ対幅の比が減少するため、気泡が発生しやすくなり、気孔がなくなります。一方、ビームの揺動により小孔も揺動し、溶融池に撹拌力を与え、溶融池の対流と撹拌を促進し、気孔の除去に効果を発揮します。
第五に、パルス周波数です。パルス周波数は、単位時間あたりにレーザービームによって放出されるパルスの数を指します。これは、溶融池内の入熱と蓄熱に影響を与え、さらに溶融池内の温度場と流れ場に影響を与えます。プール。パルス周波数が高すぎると、溶融池への過剰な入熱につながり、溶融池の温度が高くなりすぎて、高温で揮発する金属蒸気やその他の元素が生成され、細孔が発生します。パルス周波数が低すぎると、溶融池への蓄熱が不十分となり、溶融池温度が低くなりすぎてガスの溶解や抜けが減少し、細孔が発生します。一般に、パルス周波数は基板の厚さとレーザー出力に基づいて妥当な範囲内で選択する必要があり、高すぎたり低すぎたりすることは避けてください。
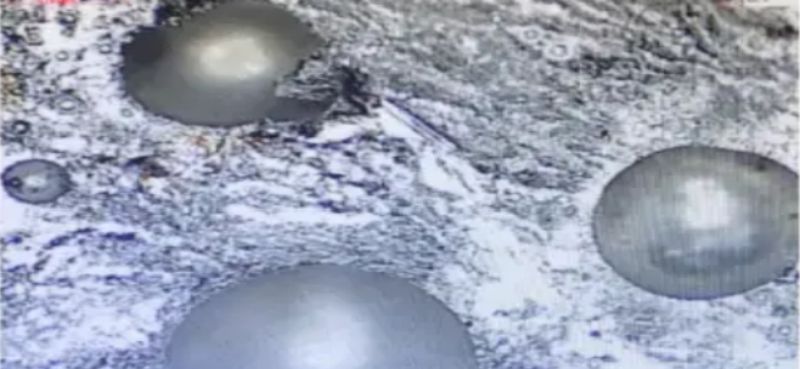
溶接穴(レーザー溶接)
2. 溶接スパッタ
レーザー溶接の溶接プロセス中に発生するスパッタは、溶接の表面品質に重大な影響を与え、レンズを汚染したり損傷したりすることがあります。一般的な性能は次のとおりです。レーザー溶接が完了すると、材料またはワークの表面に多くの金属粒子が現れ、材料またはワークの表面に付着します。最も直感的なパフォーマンスは、検流計のモードで溶接する場合、検流計の保護レンズを一定期間使用した後、表面に密なピットが現れることです。これらのピットは溶接スパッタによって引き起こされます。時間が経つと光が遮られやすくなり、溶接光の問題が発生し、溶接切れや仮想溶接などの問題が続出します。
飛沫の原因は何でしょうか?
まず電力密度ですが、電力密度が大きいほどスパッタが発生しやすくなり、スパッタは電力密度に直接関係します。これは何世紀にもわたる問題です。少なくとも今のところ、業界は飛沫の問題を解決できておらず、若干減少したとしか言えない。リチウム電池業界では、飛沫が電池ショートの最大の原因ですが、根本原因は解決できていません。バッテリーへのスパッタの影響は、保護の観点からのみ軽減できます。例えば、溶接部の周囲に塵埃除去口や保護カバーを円形に設けたり、エアナイフを円形に並べてスパッタの影響やバッテリーへのダメージを防止したりする。溶接ステーション周辺の環境、製品、部品を破壊することは手段を使い果たしたと言えます。
スパッタ問題の解決に関しては、溶接エネルギーを低減することがスパッタの低減につながるとしか言いようがありません。溶け込みが不十分な場合は、溶接速度を下げることも役立ちます。ただし、一部の特殊なプロセス要件では、ほとんど効果がありません。同じプロセスでも、機械や材料のバッチが異なれば、溶接効果はまったく異なります。したがって、新エネルギー業界には、1 つの設備に対して 1 つの溶接パラメータを設定するという不文律があります。
第二に、加工された材料やワークの表面が清掃されていない場合、油汚れや汚染物質も重大な飛沫の原因となります。この時、最も簡単なのは加工物の表面をきれいにすることです。
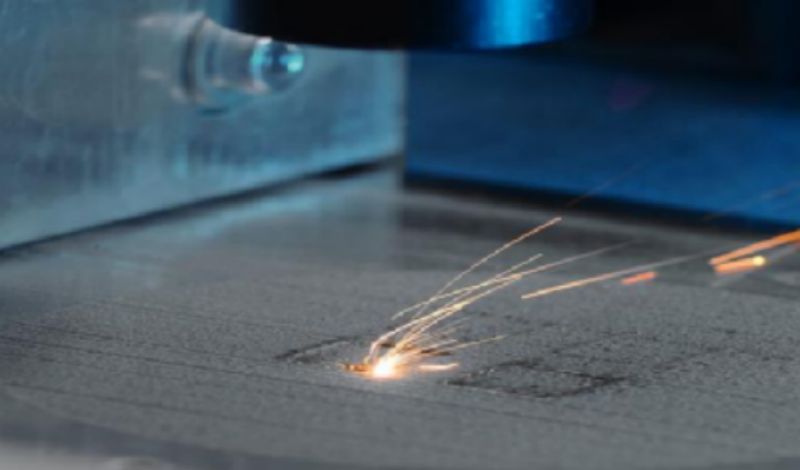
3. レーザー溶接の高い反射率
一般に、高反射とは、加工材料の抵抗率が小さく、表面が比較的平滑で、近赤外レーザーの吸収率が低いため、レーザーの放射量が多くなり、ほとんどのレーザーが使用されるためです。垂直方向 材質またはわずかな傾きにより、戻ってきたレーザー光は出力ヘッドに再入し、戻り光の一部でもエネルギー伝送ファイバーに結合され、ファイバーに沿って内部に伝送されます。レーザーの温度が上昇し、レーザー内部のコアコンポーネントが高温になり続けます。
レーザー溶接中の反射率が高すぎる場合は、次の解決策が考えられます。
3.1 反射防止コーティングを使用するか、材料の表面を処理します。溶接材料の表面を反射防止コーティングでコーティングすると、レーザーの反射率を効果的に低減できます。このコーティングは通常、レーザーエネルギーを反射する代わりに吸収する、反射率の低い特殊な光学材料です。集電体の溶接やソフト接続などの一部のプロセスでは、表面をエンボス加工することもできます。
3.2 溶接角度の調整:溶接角度を調整することで、より適切な角度でレーザー光を溶接材料に入射させることができ、反射の発生を軽減します。通常、レーザー光線を溶接する材料の表面に垂直に入射させるのが、反射を減らす良い方法です。
3.3 補助吸収剤の追加: 溶接プロセス中に、粉末または液体などの一定量の補助吸収剤が溶接部に追加されます。これらの吸収体はレーザーエネルギーを吸収し、反射率を低下させます。特定の溶接材料と適用シナリオに基づいて、適切な吸収剤を選択する必要があります。リチウム電池業界では、これはありそうにありません。
3.4 光ファイバーを使用してレーザーを送信する: 可能であれば、光ファイバーを使用してレーザーを溶接位置に送信し、反射率を下げることができます。光ファイバーはレーザービームを溶接領域に導き、溶接材料の表面への直接露出を避け、反射の発生を減らすことができます。
3.5 レーザーパラメータの調整: レーザー出力、焦点距離、焦点直径などのパラメーターを調整することにより、レーザーエネルギーの分布を制御し、反射を低減できます。一部の反射素材では、レーザー出力を下げることが反射を減らす効果的な方法となる場合があります。
3.6 ビーム スプリッターを使用する: ビーム スプリッターは、レーザー エネルギーの一部を吸収デバイスに誘導し、それによって反射の発生を減らすことができます。ビーム分割デバイスは通常、光学コンポーネントと吸収体で構成されており、適切なコンポーネントを選択し、デバイスのレイアウトを調整することで、より低い反射率を実現できます。
4. 溶接アンダーカット
リチウム電池の製造工程でアンダーカットが発生しやすいのはどの工程ですか?なぜアンダーカットが発生するのでしょうか?それを分析してみましょう。
アンダーカット、一般に溶接原料が互いによく結合していない、ギャップが大きすぎる、または溝が現れる、深さと幅が基本的に 0.5 mm より大きい、全長が溶接長さの 10% を超える、または製品プロセス標準よりも長い要求された長さ。
リチウム電池の製造プロセス全体では、アンダーカットが発生しやすく、一般に円筒形カバープレートの封止予備溶接と溶接、および正方形のアルミニウムシェルカバープレートの封止予備溶接と溶接に分布しています。主な理由は、シーリング カバー プレートはシェルと協働して溶接する必要があり、シーリング カバー プレートとシェルの間のマッチング プロセスでは過度の溶接ギャップ、溝、崩壊などが発生しやすいため、特にアンダーカットが発生しやすいためです。 。
では、アンダーカットの原因は何でしょうか?
溶接速度が速すぎると、溶接の中心を指す小さな穴の後ろの液体金属が再分布する時間がなくなり、凝固して溶接の両側にアンダーカットが発生します。上記の状況を考慮して、溶接パラメータを最適化する必要があります。簡単に言うと、さまざまなパラメータを検証する実験を繰り返し、適切なパラメータが見つかるまで DOE を実行し続けることです。
2. 溶接材料の溶接隙間、開先、崩れ等が過度に大きいと、隙間を埋める溶融金属の量が減少し、アンダーカットが発生しやすくなります。これは設備と原材料の問題です。溶接原料がプロセスの受け入れ材料要件を満たしているか、装置の精度が要件を満たしているかなど。サプライヤーや装置の責任者を絶えず拷問したり殴ったりするのが常套手段です。
3. レーザー溶接の終了時にエネルギーが急激に低下すると、小さな穴が潰れ、局所的なアンダーカットが発生する可能性があります。パワーとスピードを正しく組み合わせることで、アンダーカットの形成を効果的に防ぐことができます。古いことわざにあるように、実験を繰り返し、さまざまなパラメータを検証し、適切なパラメータが見つかるまで DOE を続けます。
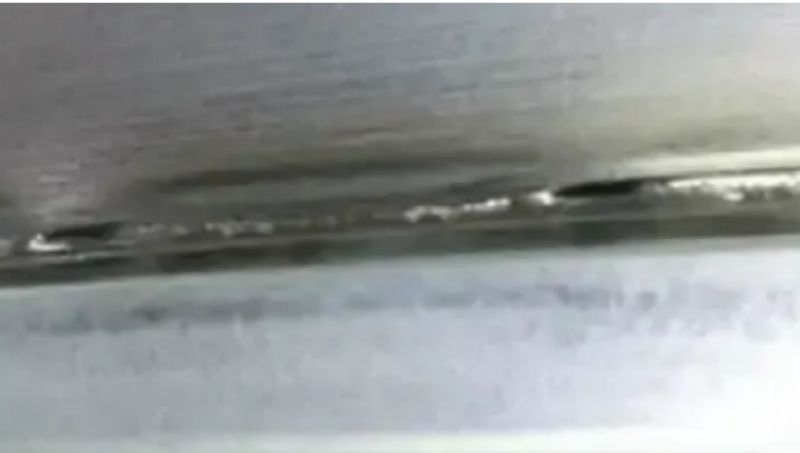
5. 溶接中心崩壊
溶接速度が遅いと溶融池が大きくなり、溶融金属の量が多くなります。これにより、表面張力を維持することが困難になる可能性があります。溶融金属が重くなりすぎると、溶接部の中心が沈み、くぼみやピットが形成されることがあります。この場合、溶融池の崩壊を防ぐためにエネルギー密度を適切に下げる必要があります。
別の状況では、溶接ギャップが穿孔を引き起こさずに崩壊を形成するだけです。これは間違いなく装置の圧入の問題です。
レーザー溶接中に発生する可能性のある欠陥とさまざまな欠陥の原因を適切に理解することで、異常な溶接の問題を解決するためのより的を絞ったアプローチが可能になります。
6. 溶接亀裂
連続レーザー溶接時に発生する亀裂は主に結晶亀裂や液状亀裂などの熱亀裂です。これらの亀裂の主な原因は、溶接が完全に固化する前に溶接によって発生する大きな収縮力です。
レーザー溶接におけるクラックの原因には次のようなものもあります。
1. 溶接部の設計が不適切:溶接部の形状や寸法の設計が不適切であると、溶接応力集中が発生し、亀裂が発生する可能性があります。解決策は、溶接応力集中を避けるために溶接設計を最適化することです。適切なオフセット溶接を使用したり、溶接形状を変更したりすることができます。
2. 溶接パラメータの不一致:溶接速度が速すぎる、出力が高すぎるなど、溶接パラメータの不適切な選択は、溶接領域で不均一な温度変化を引き起こし、大きな溶接応力や亀裂を引き起こす可能性があります。解決策は、特定の材料と溶接条件に合わせて溶接パラメータを調整することです。
3. 溶接表面の準備が不十分:酸化物やグリースなどを除去するなど、溶接前に溶接表面を適切に洗浄および前処理しないと、溶接の品質と強度に影響があり、亀裂が発生しやすくなります。解決策は、溶接面を適切に洗浄し、前処理して、溶接領域の不純物や汚染物質が効果的に処理されるようにすることです。
4. 溶接入熱の管理不良:溶接時の温度が高すぎたり、溶接層の冷却速度が適切でなかったりするなど、溶接時の入熱管理が不十分な場合、溶接部の組織が変化し、亀裂が発生します。 。解決策は、過熱と急冷を避けるために溶接中の温度と冷却速度を制御することです。
5. 応力除去不足:溶接後の応力除去処理が不十分な場合、溶接部の応力除去が不十分となり、クラックが発生しやすくなります。解決策は、溶接後に熱処理や振動処理などの適切な応力除去処理を行うことです(主な理由)。
リチウム電池の製造工程でクラックが発生しやすいのはどの工程ですか?
一般に、円筒形鋼殻やアルミニウム殻の封口溶接、角形アルミニウム殻の封口溶接などの封口溶接時にクラックが発生しやすくなります。また、モジュールの梱包工程においても、集電体の溶接でもクラックが発生しやすくなります。亀裂に。
もちろん、フィラーワイヤー、予熱、またはその他の方法を使用して、これらの亀裂を軽減または除去することもできます。
投稿時間: 2023 年 9 月 1 日